LSPI believes in giving back to our communities. We host various donation drives and volunteer opportunities throughout the year and encourage our employees to be actively involved. Through our corporate charitable contributions program, employees have the opportunity to nominate qualifying organizations for funding.
This fall, LSPI participated in the Energy Day Festival. The event was a family-friendly program that focused on science, technology, engineering and mathematics (STEM) education. LSPI hosted a booth with interactive demonstrations and explanations of drag reduction, viscosity and part per million (PPM).
This public event drew over 25,000 attendees visiting over 60 exhibitors. 184 students and teachers were recognized through the Energy Day Academic Program, granting nearly $24,000 in scholarships.
_______________________________________
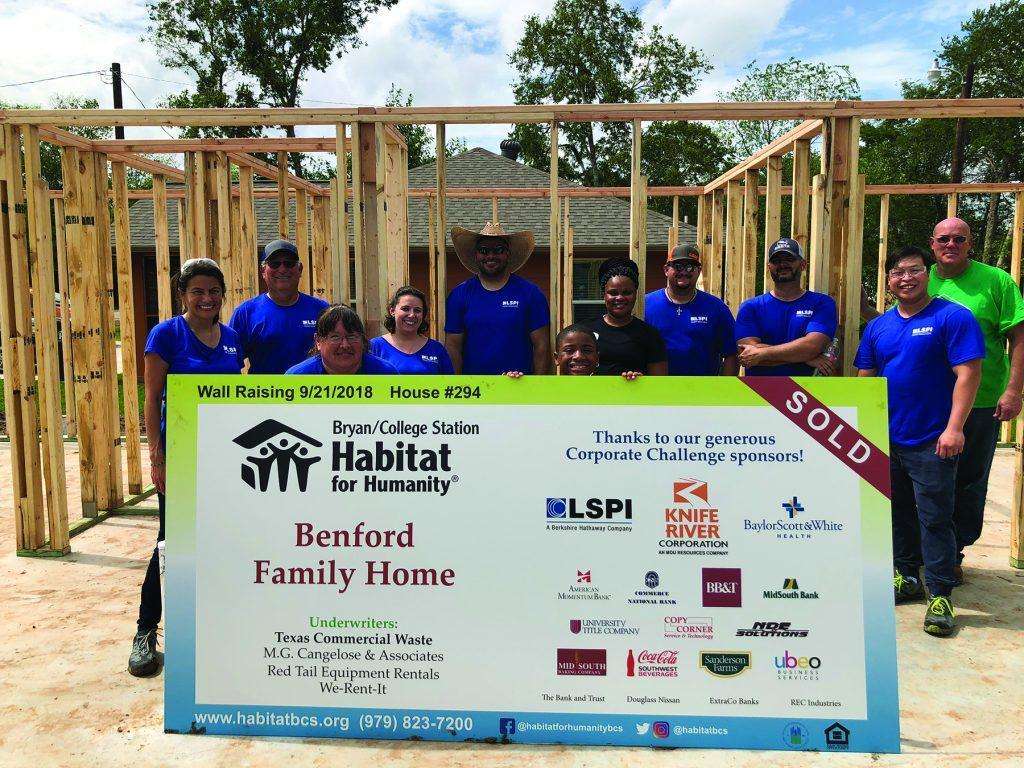
LSPI helped sponsor Habitat for Humanity of Bryan/College Station. As part of this commitment, LSPI volunteers actively participated in construction efforts and build-related activities. LSPI’s Director of Manufacturing Operations serves on the organization’s Board of Directors.
_______________________________________
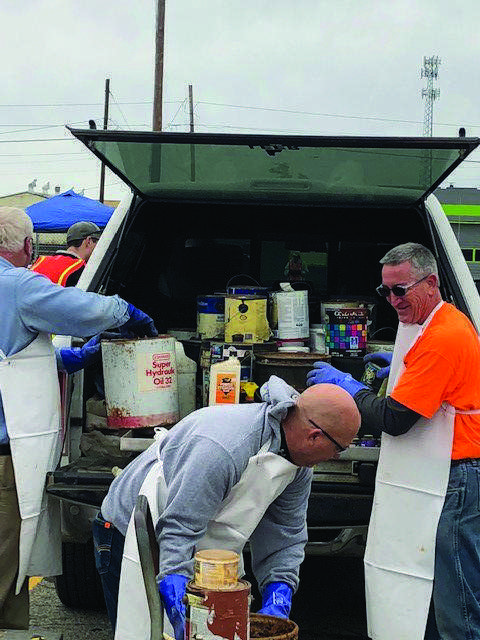
The City of Ponca City hosts a bi-annual Household Hazardous Waste Collection Day (HHWCD). This event offers the community a safe and responsible way to dispose of household hazardous waste, including used oils, car batteries, pool and household chemicals, fertilizers, electronics and medications.
_______________________________________
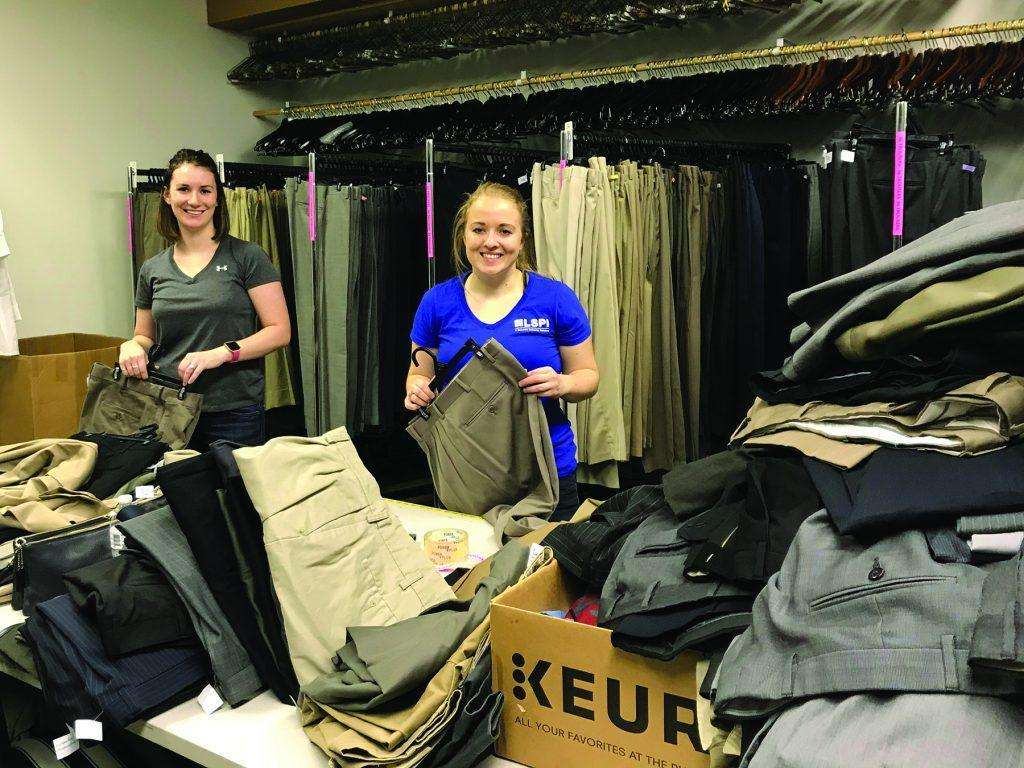
LSPI hosted a men’s clothing and professional accessory drive benefitting Career Gear Houston. Donations were hand delivered and LSPI volunteers helped sort, tag and hang incoming donations. The organization serves disadvantaged men who seek to gain employment and become role models for their families and communities.
_______________________________________
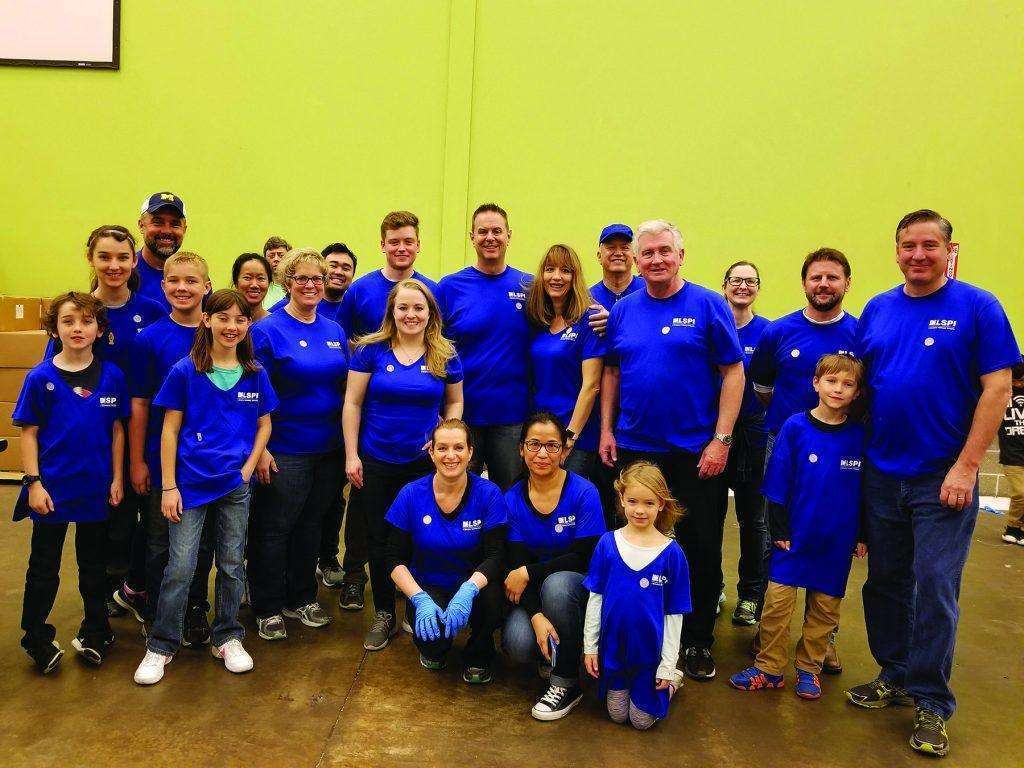
LSPI hosted a donation drive to support Houston Food Bank and organized a company volunteer shift packing food for Backpack Buddy. This program ensures that children have nourishing meals when they are away from school.
_______________________________________
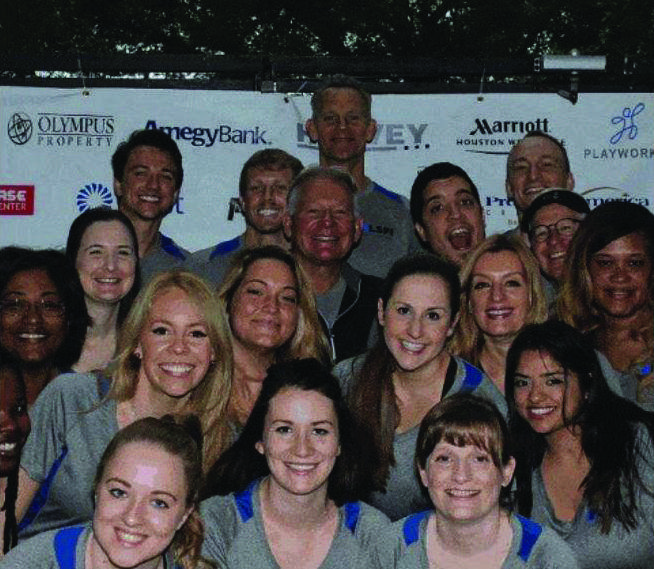
For the third year, LSPI participated in the Westchase Corporate Challenge. This event benefits The Community Fund, supporting scholarships and other educational programs.
_______________________________________
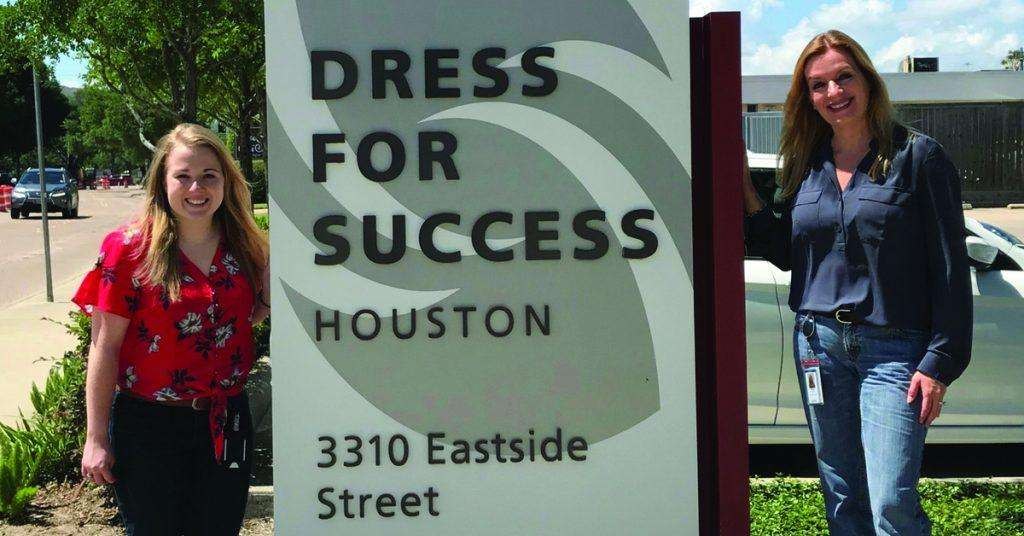
LSPI supported Dress for Success of Houston by hosting a women’s clothing and accessory donation drive. Donated wardrobes are used as part of the organization’s economic empowerment program.
_______________________________________
Houston is fortunate to have a world-renowned medical community, and many people travel the globe to see these experts. This season, LSPI employees brightened the holidays of Ronald McDonald House Houston families by donating toys and gifts.